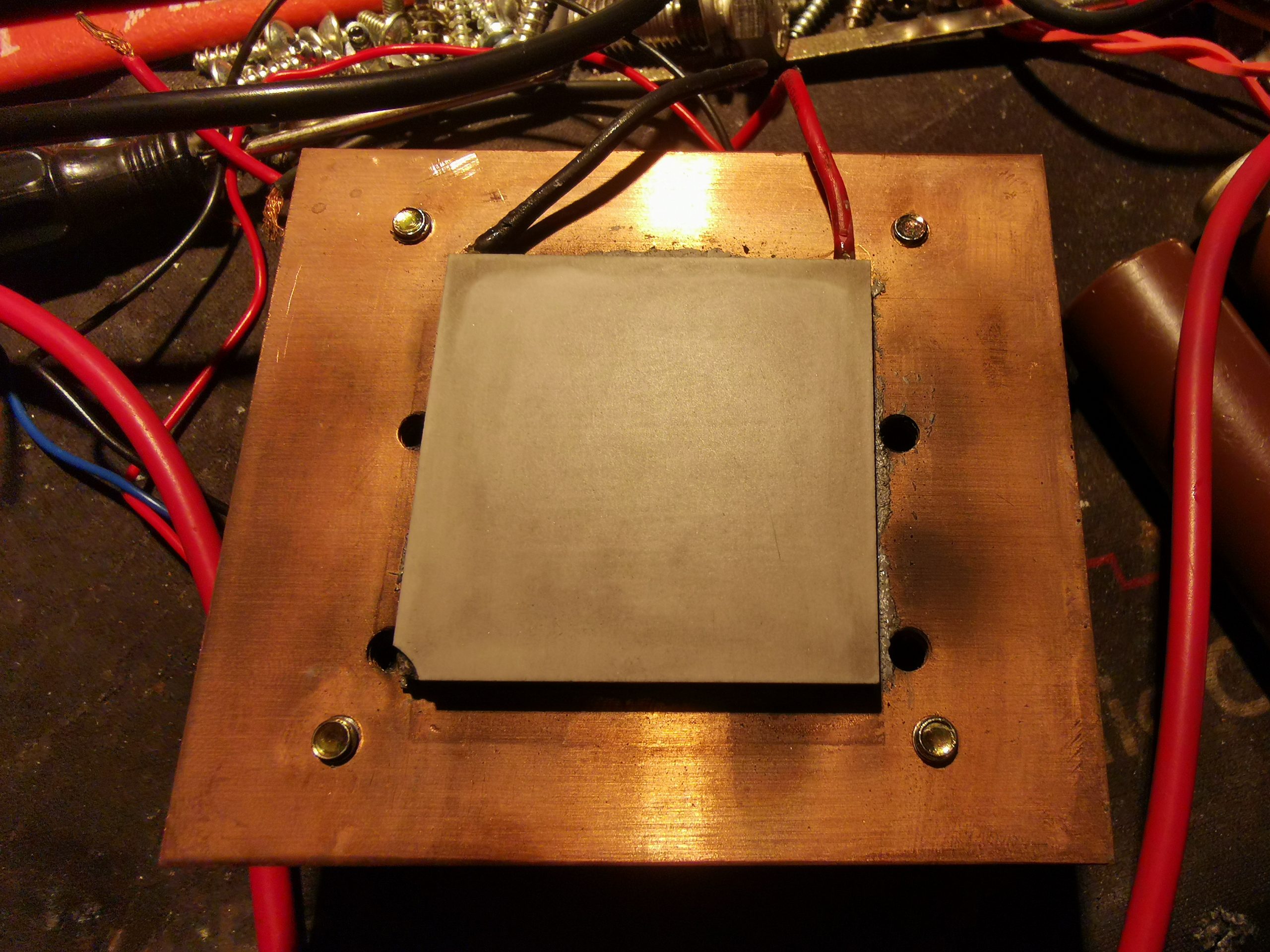
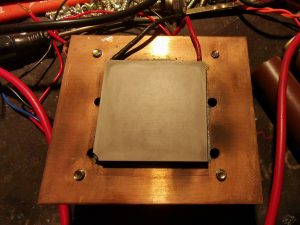
I’ve been looking for ways to build a DIY Laser Power meter for some time now, but I had no way to calibrate anything. I have been aware of DIY thermopile sensors with TECs – but no way to verify any results until now. Since I have my Gentec meter to calibrate against, I can finally get on with the project.
In the photo above, is the Peltier/TEC module mounted to the heatsink with thermal compound. In this case it’s a TEC1-12706, pulled from a cheapo dehumidifier. The cold face (with the part number printing) is against the heatsink, and the hot face will serve as the beam target. This was cleaned with solvent, and roughed up a bit with silicon carbide abrasive paper – the abrasive needs to be harder than the Alumina ceramic the module is constructed from.
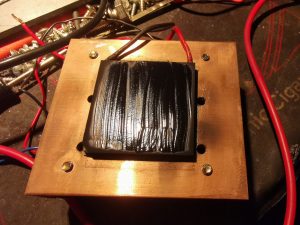
To be any good as an optical power sensor, the front face of the module needs to be coated with something to absorb as much energy from the laser beam as possible. In this case, black paint was used, as it’s completely matte when dried. Lampblack also works, and this can be coated onto a sensor face with just a wax candle, but this is far too fragile to be any practical use (being just carbon, it’s much more resistant to thermal damage from the laser beams though!).
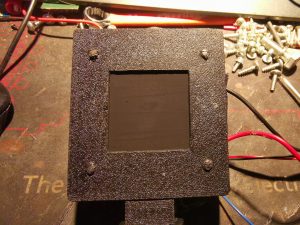
After two coats of the paint are applied to the front face of the module, the sensor head is complete. Try to get this as smooth as possible for best results. I designed & 3D printed a retention bracket for the module, and matches up with the screws that hold the fan on the finned side. This also has a block on the bottom which I threaded 1/4-20 to fit a standard tripod thread.
Like all commercial laser power sensors, the beam should be expanded as much as possible to fill the full face of the sensor. A focused high-power beam will quickly destroy the coating!
After completion, the sensor needs to be characterised. For this I set a diode module to be as close to 1W as possible, according to my calibrated meter, and applied the beam to the constructed sensor. A load impedance of 68Ω was placed across the output leads as a load. For this unit, I obtained a reading of 83.5mV/W of applied power. Even for low power levels, the fan does need to be running on the back of the heatsink, as the cold side of the sensor heating up will skew the reading.
After calibration at 1W optical power, I then ran some more tests at higher powers – 2W gave exactly double the output voltage, and throughout the power range I am able to test, the sensor seems to be entirely linear in operation.
Your sensor is just for cw lasers? Have tou ever tryied with pulsed laser stacks(808nm)?
Your sensor is just for cw lasers? Have you ever tryied with pulsed laser stacks(808nm)?
I haven’t tried with pulsed lasers – I had only intended for CW, however the thermal sensor should pick up average power without too much trouble.
Pulse power I don’t think would be possible due to the thermal mass of the sensor.
Cheers